いらっしゃいませっ!
カスタムカーショップBRENDAのこぼです(°▽°)
「FRPエアロって何?」
「ABSとFRPってどっちがいいの?」
「カーボンエアロをつけたいんだけど、、、」
初めてカスタムを依頼してくださる方の多くは、エアロパーツ系のカスタムにチャレンジします。
しかし”エアロパーツ”と一概に言っても、その材質は千差万別あり、
- FRP
- ABS
- CFRP
- PCC
- PPCC
- DCC
- CHC
- URETHANE
- ALUMINIUM
パッと思いつくだけでも9種類はあります。
もちろんすべての種類を覚えておく必要はありませんが、最低限の単語は覚えておくことをオススメします。そうしないと、
「安くカッコよく仕上げたかったのに、カスタムに想像以上のお金がかかった」
「高くてもいいからキチンと仕上げて欲しかったのに、パーツがズレまくりで不満足」
「カーボンって言ったけどなんちゃってカーボンじゃん(怒)」
みたいな結果になりかねません。
せっかくお金を使ってドレスアップやカスタムをするのに、自分の要望通りにいかないなんてちっとも面白くありません。
なので、抑えるべきポイントをサクッと覚えて、ドレスアップやカスタムの参考にして頂けたら幸いです。
カスタムカーショップの店員さんとの話し合いで使う英単語はだいたい3つです。
- FRP
- CFRP(カーボン)
- ABS
今日はこの3つの単語をできるだけ分かり易く、僕の実体験も交えながらお話していきます。
FRPパーツ
FRP=エアロ
一番最初は”アフターパーツの王様”と言っても過言ではないFRPについて紹介していきます。
FRPとは、”Fiber Reinforced Plastics(ファイバー・レインホース・プラスチック)”の略称で、”繊維強化プラスチック”を指します。
日本語に直訳すると、F=繊維、R=強化、P=プラスチックになります。
さらに噛み砕いた解説をすると、ガラス繊維や炭素繊維などの繊維(ファイバー)をプラスチックと混合し、強度を増した複合材料のことを”FRP”と呼びます。
通常のプラスチックをそのまま使うと、弾力性が無く、少し曲げよう押しただけで「パキッ」と簡単に割れてしまいます。
そこでプラスチックにガラス繊維や炭素繊維を混ぜ込み、強度と弾力性のある素材を作り上げました。
※ちなみにガラス繊維を混合する時は、ガラス繊維を細かく砕いてからプラスチックにまぶします。
後述しますが、CFRP、GFRPなどのパーツの頭文字は、使っている繊維の材質を表しています。
例えば、
A=アラミド、F=繊維、R=強化、P=プラスチック
C=カーボン、F=繊維、R=強化、P=プラスチック
G=ガラス、F=繊維、R=強化、P=プラスチック
ってな感じです。ちなみにカスタムカーショップの店員さんが、
「FRP」
と言ったときは、99%以上の確率で
「ガラス繊維のこと」
だと思ってください。
この記事でも”FRP=GFRP”の認識で解説していきます。
まぁとりあえず、“FRP”だけ覚えておけば最低限の会話は成立すると思います。
次はFRPのメリットとデメリットをまとめていきます。
FRPのメリット

1.安くてカッコいいパーツが多い
大胆なデザイン、カッコいいパーツが欲しいなら、絶対的にFRP一択です。
FRPを使ったエアロパーツはホームセンターにある材料で簡単に作れてしまいます。
つまり、製造のコストが低いので、安価でありながら、自由度の高いエアロパーツを製造することができます。
これがアフターパーツの王様たる由縁です。
製造が簡単で、価格も安いので、市場に出回っている絶対量がそもそも違うんです。
※詳しい製造方法を知りたい人は、ハンドレイアップ法、スプレーアップ法、SMCプレス法などをググってみてください。
ちなみに、FRPは雌型から剥がすとガラス繊維で表面がチクチクするので、あらかじめゲル状の樹脂を雌型にコーティングしてからプラスチックを流し込み、製造しているのが”ゲルコート”と呼ばれるモノになります。
2.パーツが破損しても安価で簡単に直せる
冒頭でもお話した通りFRPは、“繊維の集合体をプラスチックで固めたモノ”です。
ので、事故などでぶつけたとしても、破損部分に同じ材質のFRPを準備して、貼り付け、表裏にパテを埋めてやるだけで外観的な補修が簡単にできてしまいます。
あとは、塗装をするだけなので、維持費がめちゃくちゃ安いです。
もし仮にぐっちゃぐちゃに破損してもFRPは安価なので、
「買い替えればいっか(*’▽’)」
ぐらいのダメージで済みます。
ドリ車で有名な”シルビア”や”180SX”、”Z33″のアフターパーツにFRPが多い理由は、このように修復が簡単で安価だからです。
“加工が簡単=補修が簡単=お金がかからない”
これは鉄やカーボンにないとても強力なアドバンテージです。
FRPのエアロパーツが人気の理由は、パーツ本体も安い上に、補修も簡単なところにあるでしょう。さらに、
- 軽量
- 高強度
- 耐久性が高い
- 手入れがとても簡単
などのメリットもあります。
以上のことから、FRPは不動の人気を誇っているのですが、デメリットが無いわけではありません。
FRPのデメリット
パーツ精度が悪い
FRPの製造方法については先ほど解説したので割愛いたしますが、FRPパーツを作るのに特別な設備は必要ありません。
設備が必要ないので1つ1つの作業を人間が行うことになります。ので、パーツの完成度が1つ1つ違います。動画を見てもらえば分かるとは思いますが、
パーツにバラツキが出てしまうのが、FRP最大のデメリットです。
同じ会社が製造していてもパーツに個体差があるなんて事態はザラにあります。
カスタムカーショップに任せる場合はデメリットになりませんが、自分で取り付けをすると1~2週間なんて当たり前のようにかかります。
もちろんお店に任せたとしても、多少のズレは許容する必要があります。
以上を踏まえたFRPのまとめは、
・カッコいいパーツが多い
・最強のコスパを誇る
・簡単に修復できる
・長期的に使える
・パーツの精度が悪いので取り付けが大変
デメリットは取り付けが難しいぐらいなので、お店に取り付けを任せる前提でカスタムを考えているのなら、FRPは最高の選択肢になるでしょう。
CFRP(カーボン)
CFRP=LFA
先ほど説明したFRPがガラス繊維を混ぜたものならば、GFRPは炭素繊維(カーボン)を混合したモノになります。
最もCFRPのイメージが強いのは個人的には”レクサスLFA”だと思っています。
LFAのボディの約65%はCFRPで製作しています。
復習のために解説しておくと、CFRPは”Carbon Fiber Reinforced Plastics”の頭文字をとったものです。
C=カーボン、F=繊維、R=強化、P=プラスチックで、炭素繊維強化プラスチックを意味し、高い強度や剛性を得ることができる人気の素材であり、俗にいう”カーボン”って言葉で表現されています。(カーボン繊維は髪の毛よりも細いです。)
しかし、純正部品がCFRPなんて普通では考えられません。(プリウスPHVは、燃費をよくするために採用しています)理由は簡単で、
お値段がとても高いからです。
軽い、強い、超絶高い
ガラスと炭素、違う繊維を混ぜるだけで何がそんなに違うのでしょうか?
答えはとても簡単です。
ガラス繊維の化学式は、CaNaO4P
炭素は元素なので、C
各元素の比重を確認するまでもなく、ガラス繊維に比べて炭素の方が
“aNaO4P”分軽い
のです。
強度に関しては、元素である炭素のみでできたカーボンの方がガラス繊維よりも3倍以上頑丈です。
イメージするならCFRPは鉄の1/5以下、アルミの1/2の軽さを誇り、ガラス繊維よりも3倍以上頑丈なのです。
そんなに軽くて最強に頑丈なパーツは一体いくらするのでしょうか?
・・・
・・
・
ガラス繊維の5~10倍の値段です。
カーボンパーツは工程や手間がかかるうえに、職人ワザといえるハンドメイドの作業が中心です。
なので、CFRPは
「お金より軽さを追求する」
レーシングガチ勢が愛するイメージが強く、一般ユーザーには縁遠いイメージがあります。
しかし、男らしい素材感とレーシーなルックスはどうしても男心をくすぐり、ついつい眺めてしまうモノです。
そんなCFRP業界を揺るがすテクノロジーが最近日産から飛び出しました。
これでカーボンが僕たちの身近な存在になるかもしれません。
1パーツ2日かかっていたものが、2分になった。
最近何かとネガティブなイメージが付きまとう日産でしたが、ここにきて破壊的なイノベーションを見せてくれました。
ハンドメイドの技術がなくなるワケではないけれど、この技術が日本の企業間でシェアされてば、CFRPのパーツが劇的に安くなります。(課題は山積みですけどね)
日産自動車は2020年9月3日に「CFRP成形の新技術」に関する発表を行いました。
これは近い将来の電動化モデルに向けた、パーツ量産における新提案であり、業界を震撼させました。
CFRPパーツは、成型の際には数多くの工程を踏む必要があります。
炭素繊維に樹脂を染み込ませる”含浸”ひとつとっても、手作業による塗り込みや機械による流し込みがあったり、大きな窯で焼くオートクレーブや、金型を用いた圧縮によって型取る方法など多種多様で、仕上がりにもムラが出てしまうのがネックです。
材料の単価が高いのもそうだが、工程に多くの時間が割かれ、それに伴い労力も割かれるため、結果的にCFRPパーツは高価なものになってしまうのです。
そこで日産は、
「工程まとめればいいんじゃね?w」
という発想から、「C-RTM(Compression Resin Transfer Molding)」という工法を編み出しました。
このC-RTM工法は、金型を用いた型取りをしつつ、同時に加圧し均等に含浸させながら成型するというもので、樹脂を流し込む際の温度変化や浸透性など“流動解析”を行い、均等な流し込みを可能にしつつも、適切な強度を確保し、作業時間を短縮した点が素晴らしいのです。
C-RTM工法を用いれば、同じ時間で数倍の数のパーツを生み出すことが可能になりました。
製造コストが抑えられれば、パーツ単価も下がってくるのは間違いないと思います。
日産自動車は、
「この技術で作り上げた構造部材を2024~2025年に登場予定の新型EVに採用する」
と明言しているが、次期GT-Rや、NISMOなどのスポーツカーなどへも間違いなく使われると考えています。
なぜなら、アルミやハイテン鋼、そしてCFRPの組み合わせによって車両全体で80kgのダイエットが実現できるのですから、横展開しない訳がありません。
さて、そんな身近な存在になるそうなCFRP(カーボン)ですが、2つの種類に分岐しているので購入を検討する場合は必ず覚えておきましょう。
ECC or DCC (ドライカーボン)
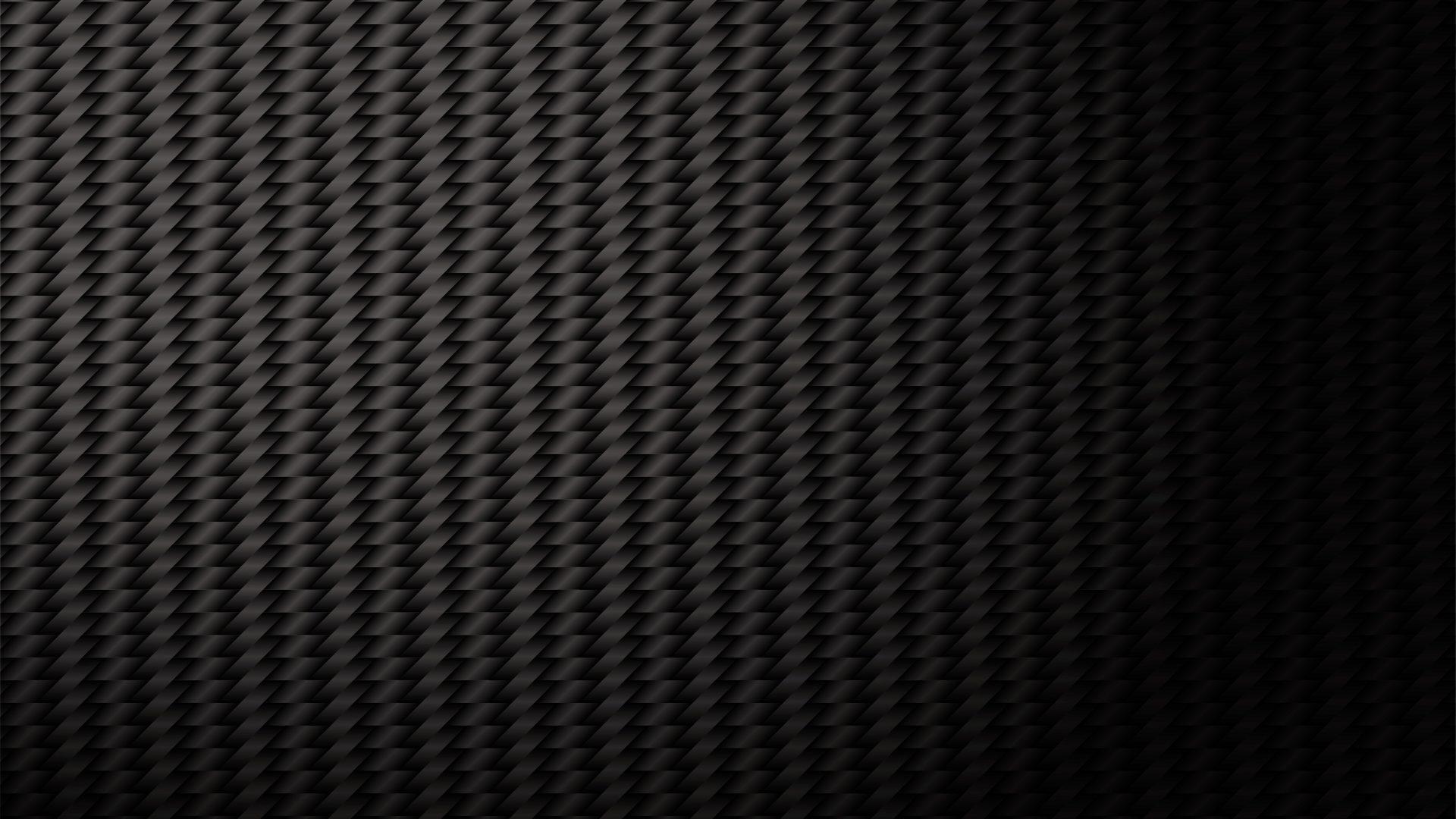
本物の軽量化
ドライカーボンの正式名称は、ECC(エポキシ・カーボン・コンポジット)と言います。
E=エポキシ、C=カーボン、C=合成
です。(※エポキシ樹脂…熱硬化性のある液体)
または、DCC(ドライ・カーボン・コンポジット)と呼ばれています。
今まで説明してきたCFRPのメリットを忠実に再現しているパーツがドライカーボンになります。
製造方法は、エポキシ樹脂を炭素繊維に染み込ませて、シート状にし、ミルクレープのように何層にも重ね合わせ、真空バックで内部の空気を抜き、オートクレープで加圧と過熱をして硬化させ、成形させます。
最小限の樹脂のなかに繊維がぎっしり詰まった状態になるので、
超軽量、
耐熱温度無敵、
機械的強度最強。
F1、ハイパーカー、スーパーカーに使われているカーボン素材は、すべてドライカーボンになります。
炭素をフルに使うことで、炭素の恩恵がモロにパーツの恩恵に繋がります。
製造工程を見て感じ取った人も多いと思いますが、製造に特別な設備が必要で、手作業も多く、材料の単価も高いため、非常に高価になってしまいます。
ドライカーボンを視野に入れる人は値段なんて気にしてはいけませんw
余談になりますが、カーボン製品にはコスト以外に、リサイクルに不向きという欠点もあり、近年エポキシ系樹脂の代わりに、ポリアミド(PA)やポリプロピレン(PP)などの、熱可塑性樹脂に変えた”熱可塑性CFRP”の開発にも注目が集まってきているので、気になる人はチェックしてみると面白いでしょう。
ちなみに、熱可塑性CFRPは樹脂の価格が安く、生産性が高いのが特徴な上に、リサイクルも可能なのでとてもエコです
でも、現状では寸法精度が課題らしく、未来のマテリアルって感じですかね。
ちなみにカーボンファイバーは、日本人が発明した製品で、東レ、帝人、三菱レイヨン(現三菱ケミカル)が、世界の3大炭素繊維メーカーといわれています。
一般人で買える最上位が、ドライカーボン。
と、覚えておきましょう。
PCC(ウェットカーボン)
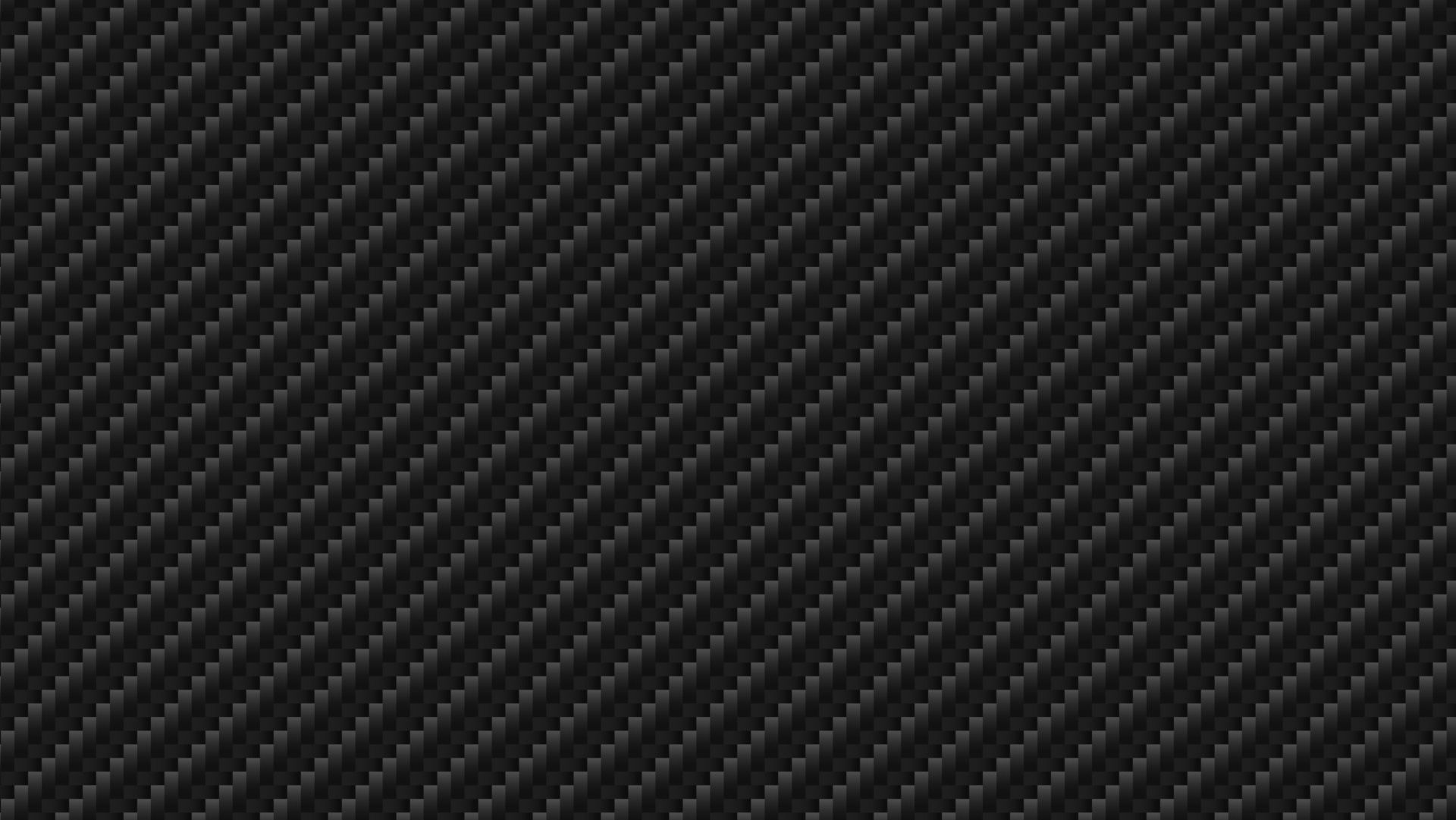
なんちゃってカーボン。
CFRPの98%以上は、ウェットカーボンだと考えて良いです。
PCC(ポリエステル・カーボン・コンポジット)と呼ばれており、P=ポリエステル、C=カーボン、C=合成の意味を持ちます。両者の違いを簡単にイメージするなら、
ドライカーボンは、”ピニンファリーナ“が作った椅子
ウェットカーボンは、”ニトリ“が作った椅子
ぐらいの違いがあります。
明確な違いはカーボンの使用量と、カーボンに染み込ませる樹脂です。
ウェットカーボンは、安価なポリエステル樹脂を大量に使っているため、特殊な設備が無くても製造可能です。
何よりカーボンの使用量を抑えることで価格も抑えているので、ドライカーボンに比べると価格も性能は雲泥の差です。
「表面・カーボン、裏面・グラスファイバー」
みたいな感じで作られています。中には、中身はガラス繊維で、その上にカーボンシートを貼り、”ウェットカーボン”として売りに出されている製品もあります。
ゆえに”なんちゃってカーボン”と僕は呼んでいます。
平面で大きな加工が必要ないエンジンフードやルーフ、GTウイングなどはウェットカーボンのパーツが多く販売されており、軽量化と共にカーボンの織り目で〝イジってる〟感を演出してくれます。
レースで使われるガチに軽量なドライカーボンとは全く別物ですので、あくまでウェットカーボンはドレスアップ用と認識しておいてください。
他にも、炭素繊維の折り方が綾織りのモノは、だいたいウェットカーボンです。理由は、斜めに模様が入るため、見た目が良いからです。(ドレスアップ系エアロに使われます)
逆に、平織りになっているカーボンパーツは、ドライカーボンの可能性が高いです。(強度が高いから)
画像を見返してみるとドライとウエットで網目が違うことに気が付けると思います。
ここまでウェットカーボンを若干ディりましたけど、FRPよりは100%優秀な製品であることに違いはありません。
普通の人は、ウェットカーボン。
と、覚えておきましょう。
CHC(カーボン・ハニカム・コンジット)
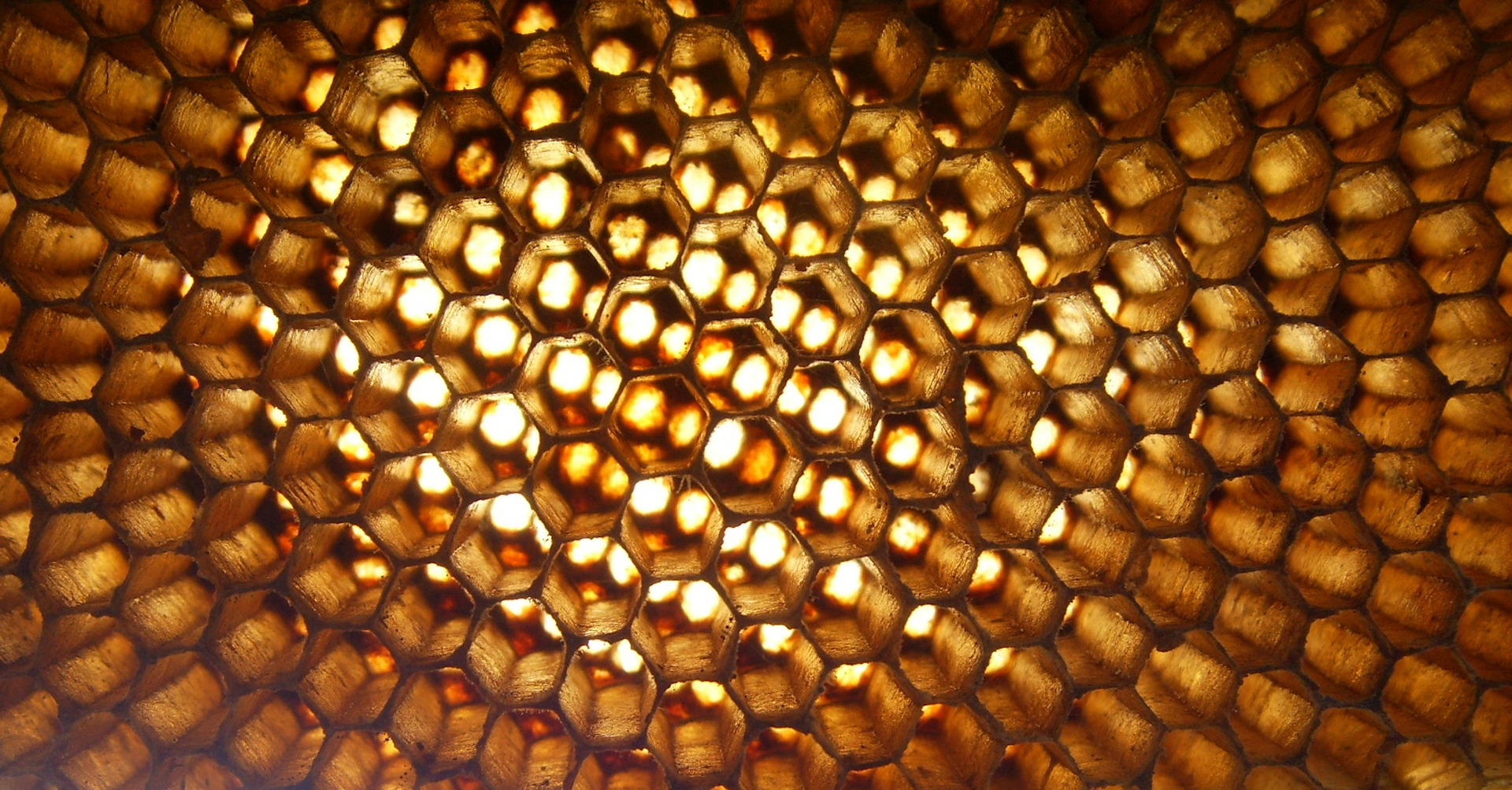
このレベルになってくる、一般では手に入らなくなってきますし、家が建つレベルの話になってくるので参考程度に覚えておいてください。
C=カーボン、H=ハチの巣、C=構造
の意味を持ちます。想像に難しくないとは思いますが、構造がハチの巣型になっているので”カーボン・ハニカム・コンジット“の名になっています。
ハチの巣構造を使っている理由は、平面充填(平面を隙間なく敷き詰めること)できる図形の中で外周の長さが等しく、面積が大きくなるハチの巣構造が採用されています。
※原子レベルにおいても、炭素同士が六角形に結合すると、あらゆる原子結合で最も強いことがわかっています。
肝心の製造方法は、薄いカーボンの層2枚の間に、蜂の巣状の薄い縦壁を無数に挟み込み、超軽量かつ最凶の強度を実現しています。
このレベルになると、飛行機や戦闘機に使われるレベルで軽くて強いので、F1マシンのシャーシなどに使われることが多いです。
まっ、参考程度に頭の片隅にでもおいておいてください。
ドライカーボンの上位互換ぐらいに覚えておいてください。
変態は、ハニカムカーボン。
と覚えておきましょう。
最後にCFRPについてまとめおきます。
・ドライカーボンが、真のカーボン。
→超軽量
→高強度、高剛(耐摩耗性、耐熱性、耐酸性、導電性)
→たわみにくい
→バカ高い
・ウェットカーボンは、下位互換。
・ハニカムカーボンは、超絶ガチ。
ぐらいに覚えておくのがちょうどよいですかね(‘ω’)ノ
CFRPの大枠に、ドライカーボン、ウェットカーボン、ハニカムカーボンが分岐しているイメージを持ちましょう。
さて、お次はABSについて解説していきます。
ABS(アクリロニトリル・ブタジエン・スチレン共重合樹脂)
FRP vs ABS
ネットの世界ではよくこの図式をよく見ますが、両者とも全く違う方向性なので注意してください。
ABSは、アクリロニトル・ブタジエン・スチレンの略で、それぞれの意味は、
A=アクリロニトリル、B=ブタジエン、S=スチレン
というように、原料である3つの樹脂がそのまま名前になったプラスチック素材になります。
ちなみに、
A=アクリロニトリルは、アクリル繊維の原料で、強度・耐久性が強い。
B=ブタジエンは、合成ゴムに使う材料で、耐摩耗性、耐衝撃性、耐熱老化性に優れている。
S=スチレンは、合成樹脂。
FRPでは、繊維+プラスチックなのに対し、ABSは、繊維+ゴム+アクリル+合成樹脂なのが最大の違いです。
ABSのメリット
ABSは、強度・耐久性が高く、ゴムのように弾力、耐衝撃性に優れているパーツになります。
繊維にゴムを混ぜているので加工性が高く、寸法安定性に優れていることから、真空成形機を使用しての大量生産が可能です。
その為、純正オプションの外装部品、メーカー純正のエアロパーツなどに使われるケースが多いです。
大量生産でコスト削減は出来ているのですが、結局は機械を使っての製造になるので、FRPに比べてコストがかさみ価格は高くなります。
補修に関しては、FRPと同様に直せはするのですが、
「自作で直せるっしょ(; ・`д・´)」
みたいなノリでは簡単に直りません。
ABSは有機溶剤に溶けやすいので、補修ではそれを上手く生かし、アセトンなどで破断面を溶かしてくっつけ、修理の下地にしてから補修します。
この作業が難易度高めなので、素直にお店に依頼することをオススメします。
パーツの精度がとても高い
機械での製造が可能なのでパーツの精度は最高に良いです。
例えば、少しでも寸法が狂ってしまうと見栄えが悪いヘッドライトのアイラインのような部分、曲面に貼り付ける必要のあるパーツは、ABSの方が合わせやすいです。
純正パーツとして使われている以上、精度に関しては文句のつけようがないぐらい素晴らしいものがあります。
FRPとABS、カーボンの違いについて

この記事で最も大切な部分になります。
まずは、FRPのメリットとデメリット、特徴をまとめてみましょう。
・F=繊維、R=強化、P=プラスチック
・最強のコスパを誇る(メッチャ安い)
・簡単に修復できる
・カッコいいパーツが多い
・パーツの精度が悪いので取り付けが大変
デメリットは、精度が悪いことによる取り付けの難しさです。
なのでFRPを検討する場合は、お店に取り付けを任せる前提でカスタムを考えている人向けですね。
・A=アクリロニトリル、B=ブタジエン、S=スチレン
・精度がクソ高いので取り付けが簡単
・ゴムが混ざっているので強度が高い
・自分で修復するのは難しい
・派手で奇抜なパーツは少ない
・設備を使っての製造なのでFRPよりは価格が高い。
デメリットは、価格がFRPに比べて高い上に、奇抜で派手なパーツが少ないことです。
なので、価格の折り合いがつかない、もしくは好みのパーツが無い場合はFRP系を選ぶか、諦めるしかありません。
奇抜で派手なパーツが少ない理由は、機械的なコストをかけてあまり売れないパーツを作っても企業は儲からないので、需要が多く人気の高い定番のパーツを作るのは当たり前のことだと言えるでしょう。
念のために、CFRP(カーボン)についてもまとめておきましょう。
・C=カーボン、F=繊維、R=強化、P=プラスチック
・ドライカーボンが、真のカーボン。
→超軽量
→高強度、高剛(耐摩耗性、耐熱性、耐酸性、導電性)
→たわみにくい
→バカ高い
・ウェットカーボンは、ドライの下位互換。
・ハニカムカーボンは、超絶ガチで一般人には無理。
デメリットは、パーツがバカ高いことです。
さて以上のことを踏まえて、あなたはどのパーツを買うべきか診断していきます。
【価格重視→FRP】
価格を重視するならFRPの右に出るモノはいません。
しかもカッコいいからFRPはマジで最高です。
【コスパ重視→ウェットカーボン】
コスパが何を意味するのか、それによって話は変わってきますが、費用対効果という意味で考えるならば一番はウェットカーボンです。
カーボン調って間違いなく満たされます、自己満足。
【タイム重視→ドライカーボン】
速度をどこまでも突き詰めたい人向け。
お金は、、、気にしないでくださいw
【DIYしたい派→ABS】
自分の家で取り付けたい人は、パーツ精度の良いABS一択。
ちなみにどのパーツにも説明書に書いてありますが、
「パーツの取り付けはプロの方に依頼してください」
と書いているので、あくまで自己責任で取り付けはするようにしましょう。
ちなみに知っているとは思いますが、間違ってもドライカーボンをDIYで付けるようなことは避けてください。
つけ方が少しズレるだけで風の抵抗が変わり、本来の恩恵を捨てることになります。
高いパーツほどお店を頼るようにした方が賢明な判断だと個人的には思います。
まとめ

繰り返しになりますが、
価格=FRP
コスパ=ウェットカーボン
タイム=ドライカーボン
DIY=ABS
になるのですが、結局は
自分が好きなパーツをつけよう(゚Д゚)ノ
って結論に帰結します(笑)
自分のクルマぐらい、自分の価値観で仕上げて良いと思います。
問題はお財布のひもをどこまで緩めることができるのか、だけそれだけです。
この悩む時間も含めてカスタムなので、ぜひじっくりとたっぷりと時間を使って悩んでみてください。
ココからは超絶マニアックなパーツの材質について解説していきます。
PP(ポリプロピレン)
現在の主流はPP(ポリプロピレン)
一番最初に説明したFRP、ABSなどももちん使われていましたが、FRPやABSは破損した際に鋭い断面ができるという欠点があります。
その欠点がないのがポリプロピレンなので、バンパー素材としてはポリプロピレンが総合的に優れているという判断が現在の主流です。
ほどよく柔軟で、成型しやすく、衝撃に強く、割れにくい。もし割れても安全な割れ方をする。修理はもちろん可能で、リサイクルもできる。
そりゃ各メーカーがスタンダードにしたくなるよね、ってお話です。
ALUMINIUM(アルミニウム)
アルミ=NSX
アルミニウムはご存じ1円玉に使われているとても軽くて柔らかい金属です。
鉄や銅に比べて約1/3、チタンに比べても40%も軽い為、軽量化・省エネ化に役立っています。
アルミニウムはその柔らかさを活かし、形を複雑にすることができるメリットがあるので、パーツの点数を少なく設計することができる為、重量を抑えながら強度を保つことができます。
何度も言いますが「軽量は正義」です。
走行性能、燃費、何をとっても車は軽ければ軽いほど良いモノです。
海外ではフェラーリのモデナ、アウディのR8、A8、そしてTTなどにアルミニウムは採用されています。
日本では初代NSX、初代インサイト、そして新型NSXに採用されています。
なぜ日本ではホンダだけがアルミを採用しているのでしょうか?
その秘密は電力が大きく関係しています。
アルミの加工に莫大な電気を使う
ご存じの方も多いかもしれませんが、日本の電気代はアメリカの4倍以上も高いです。
アルミニウムの原材料であるボーキサイトからアルミニウム地金を製造・加工するには、それはそれは莫大な電力が必要になります。
電気料金の安い国で加工できなければ、アルミニウムを使う恩恵以上にコストが肥大します。つまりは価格がバカみたいに上がったり、採算が取れなくなってしまうのです。
その証拠に初代NSXと初代インサイトが生産されていた栃木県にある高根沢工場は、新たな変電施設を新設するほど製造に多くの電力を必要としていました。
ちなみに現行のNSXは、電気料金の安いアメリカのオハイオ州で製造されています。
ビットコインのマイニングが日本で行われない理由も同様で、日本の電気代があまりにも高く採算が取れないからです。だから、電気代の安い中国やアメリカでマイニングが盛んにおこなわれているのです。
少し話はそれましたが、仮にアルミニウムのカスタムパーツが出てきたとしても、現時点ではオススメできません。
仮に飛び石や事故でアルミニウムが変形してしまった場合、鉄の5倍近くのお金と時間をかけて修理することになります。
バーナーで熱を入れると溶けてしまうし、ハンマーで叩くと伸びてしまうので、直すにはかなりのテクニックと時間が必要です。
実際にアルミニウムのリアバンパーをハンマーでへこませて、修理に出してクレイジー野郎がいたので、気になる方は動画をチェックしてみてください。
アルミニウムについての見識をさらに深めたい人は、日本軽金属㈱ グループ技術センターが出している報告書をご覧ください。
URETHANE(ウレタン)
無塗装=ウレタン
ウレタンフォームと呼ばれる石油原料を用いた化学合成材になります。動画を見てわかると思いますが、
アメ車で踏みつぶしてもグニャングニャンになるほど柔軟性が高い
というのが最大の特徴で、その他の性能についてはFRPとほとんど同じになります。
今でも現行車に採用されており、新型ジムニーやマツダCX-5、CX-30といったSUVに無塗装のウレタン製パーツが積極的に採用されています。
しかしこのウレタンという材質、石油を使っているのでリサイクルができず、燃やすと黒煙を上げ、環境的に問題アリです。
さらに、ウレタン製の塗料は他に比べると特殊なので少し高いです。
おまけに、長い期間使っていると縮みますし、はげて白みますし、夏と冬で大きさが変わります(笑)
ので、多くのウレタン製のバンパーなどは塗装の工程をしません。四季のある日本で塗装をしても結局は塗装割れを引き起こすからです。
そんなリスクを冒すぐらいなら無塗装で出した方がコストを抑えられます。
FRPに敗れたウレタン
ウレタンがあまり使われていない理由は、社会の問題点とウレタンの問題点がちょうど合致してしまったからです。
平たく言えば、エネルギー効率が悪い上に、処理するたびに大量のCO2を排出するので、日本のお家芸である自動車メーカーは環境に配慮してほとんど使わなくなりました。
おまけに無塗装なので、あからさまに「コストを下げてます」と言わんばかりの見た目になってしまうので、乗用はもちろん商用車でも採用するモデルは少なくなっています。
以上、車に使われるパーツの材質や素材の多さがおわかりいただけたでしょうか?
車業界の未来はまだまだ面白くなりそうです( ゚Д゚)
でわまたっ。
告知:「BRENDA 公式LINE」を始めました。
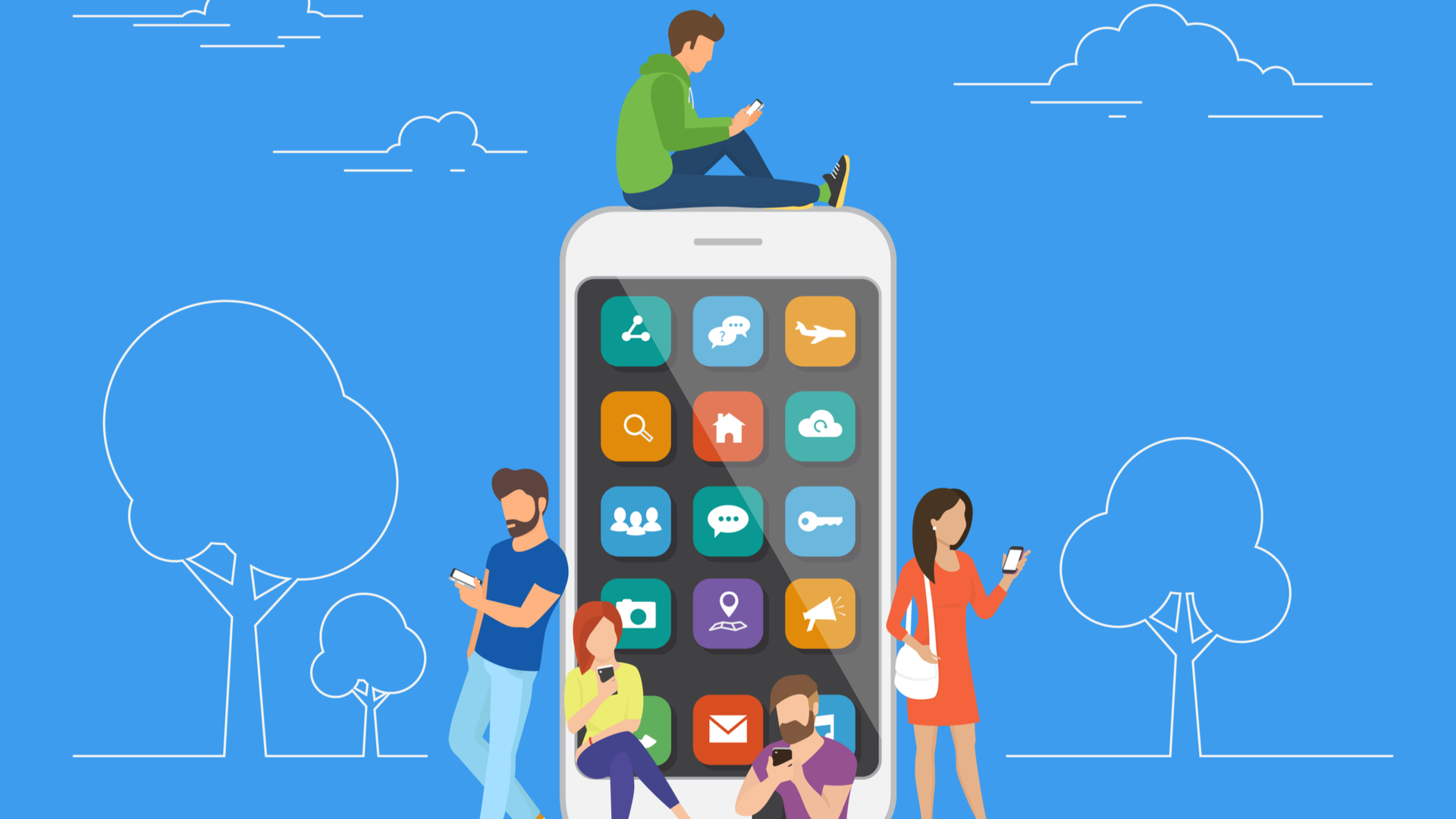
現在「BRENDA LINE公式」と友だちになると、「オイル交換が無料になるショップカード」や、ヘッドライトスチーマーが半額になる「片目無料クーポン」など、お客様のカーライフをサポートする特典を数多く準備しております。
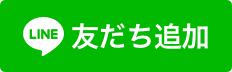
もし使い方に不安のある人は【BRENDA LINE公式アカウントのご案内】をご一読ください。
コンテンツ作りの励みになりますので、「見て良かった( ゚Д゚)」と感じた人は”チャンネル登録”よろしくお願いします。